Introduction
In order to share the activity of the Letterpress Goes 3D, or LG3D, we first must share the definition and potential of “letterpress.” Letterpress was the dominant printing technology from the 16th century to the early 20th century, and continues to be used today for educational, historical, and artisanal purposes. In letterpress printing, individual pieces of movable, metal type are arranged and secured in a frame—called a chase—which is then secured in a press. A wide variety of presses have been used throughout the centuries, but all operate on a similar principle: the type, “locked-in” to the frame, is inked either by hand or by rollers, and the press then presses paper against the inked type surface in order to create a print.
Using letterpress, printers can print both alphanumeric characters and images. Images are usually printed through use of metalcuts and woodcuts, with mirror images etched onto their surface that appear right-facing when printed. Metal or woodcuts have been created for a huge range of purposes and used in a vast variety of ways, from advertisement to education, from news reporting to fanciful illustration, from ornamentation to instruction.
A large part of LG3D’s mission is to work toward solving three issues surrounding letterpress cuts today. First, in many cases, while we may still have archival access to the printed images that historical cuts created, the cuts themselves have been lost to time. Second, though surviving cuts do showcase a wide variety of imagery, very few letterpress cuts have been created since the first half of the 20th century, leaving a gap in the sorts of images available for printing today—if you wanted to print an image of a mobile phone, for instance, you’d be out of luck using historical cuts. Something similar could be said of fonts; there are a huge range of useful, creative, and accessible fonts today that exist digitally, but not as moveable type that can be used in letterpress printing.
The Letterpress Goes 3D project works to resolve these three major gaps. Begun in Spring 2020, LG3D uses 3D printing, laser cutting, and other modern technology to reverse engineer historical woodcuts and metalcuts and develop new woodcuts based on contemporary designs. LG3D is housed in the Northeastern University English Department’s Huskiana Letterpress Studio, and is led by Professor Ryan Cordell and PhD Candidate Kenneth Oravetz, with significant support from engineering undergraduate Smeet Patel and engagement with the Northeastern community. Together, the LG3D team has developed ways to accessibly, efficiently, and precisely recreate woodcut and metalcut blocks from historical printed images, and make new blocks of contemporary images, for usage in the Huskiana Letterpress Studio and beyond. The following section details our achievements during the 2020-2021 academic years. Following that section, we detail what LG3D can offer to educators, creators, and researchers; one of our primary goals in the coming year is to ensure we offer LG3D and letterpress opportunities to students and faculty throughout the university. We conclude with some of LG3D’s additional goals for the future.
Our Achievements Thus Far
The first year of LG3D was dedicated to working with digital tools and campus collaborators to determine best practices for creating (wood, metal, or other material) printing blocks, henceforth referred to simply as “blocks.” In the process, LG3D created blocks with pedagogical, creative, and community value. LG3D focuses on creating blocks using two different methods: laser cutting, wherein a digitized image is carved onto a piece of wood using a specialized, automated laser cutter, and 3D printing, where a digitized image is turned into a 3D model that is then printed using a 3D printer.
Laser Cutting
Over the course of Fall 2020, and despite the limitations of the Covid pandemic, LG3D refined and finalized its process for designing, laser cutting, and ultimately letterpress printing woodcut blocks. Laser cutting is a useful method for creating durable, precisely rendered, and clean-printing blocks. The primary limitations of laser cutting is that this method requires woodworking equipment and expertise in order for the laser-etched pieces to be properly cut to letterpress dimensions. LG3D has collaborated with Patrick Kana and the Northeastern College of Art, Media, and Design Makerspace for the specialized laser cutting technology and woodcutting tools necessary for creating these laser cut wood blocks.
The blocks LG3D has laser cut fall into three categories: historical images, contemporary images, and fonts. Each category requires a distinct process for digitally designing the image to be laser cut; descriptions of each of these processes can be found on the Huskiana website (historical, contemporary, and fonts are linked here). Broadly speaking, for each process, we take a photograph of, scan, or—in the case of digital images—use the original file for the desired design for woodcutting; process it to align it for proper etching and printing, and to remove imperfections and extraneous details; and then convert it into a vector image that can be resized without loss of fidelity and which the laser cutter can properly “read” in order to etch the design into wood. Once the design is complete, we send it to the Makerspace, where they laser etch the design into wood, and then cut the wood block to proper letterpress height, .918 inches. We then sand and clean the woodcut block before using it in Huskiana letterpress.
We have used laser cutting to create wood blocks of the following designs:
- Historical
- Thomas Nason’s woodcut of the Boston Public Garden
- Letters from the University of Minnesota collection of initial capitals


- Contemporary
- The Northeastern University husky logo and seal
- Fonts
- A font designed by student Emma Farman, replicating the fonts seen on WPA National Parks posters
- Letters in Kuchen, Demode, and pixelated fonts

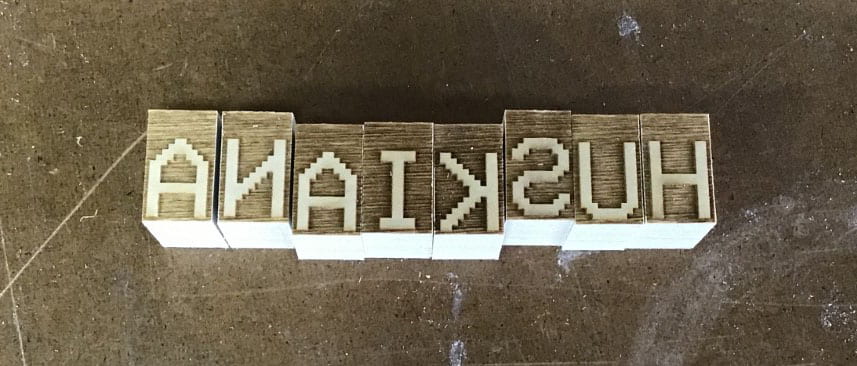
We also have designs in the pipeline of early modern memetic images from UC Santa Barbara’s Broadside Ballads Archive, social media logos for usage by Northeastern community groups and event notices, emoticons, ornamentation, comics imagery (panels, word balloons), and additional fonts.
3D Printing
LG3D also refined its process for 3D printing blocks over the course of Fall 2020. 3D printing is an accessible method of creating letterpress blocks, especially at Northeastern University. Unlike laser cutting, 3D printing does not require access to woodworking materials, space, and expertise. While it does require a 3D printer, the Northeastern Library provides 3D printing services for students; all students need to do is send their design to the Library and the Library will print it. This makes 3D printing an excellent method for creating block designs for limited, personal, or highly specific usage, such as for class assignments and personal creative projects. Most designs oriented toward individual projects should be 3D printed. The downside to 3D printing is that 3D prints are less durable and precise than their wood engraved counterparts, and can take a bit longer to digitally design. However, these limitations do not hamper the print effectiveness of the blocks to a significant degree for the vast majority of users. It also takes a very long time to 3D print. While the actual 3D printing process is a hands-off process, its length makes it impractical for creating full fonts, which can be laser cut in much less time. Smeet Patel has been conducting extensive tests to determine ideal 3D printer settings for 3D blocks of all varieties and designs.
Designs to be 3D printed go through a similar process as the laser cut designs. The most significant difference is that once a 2D design has been created, it must be then turned into a 3D model using a CAD (computer-aided design and drafting) software. We use TinkerCAD because of its emphasis on simplicity and accessibility, which allows students to more easily create their own designs. Our guide for 3D printing is forthcoming; this post will be updated with a link once it is available.
We have used 3D printing to create letterpress-printable plastic blocks of the following designs:
- Historical
- Acorn, a woodcut by Thomas Nason
- A Mother Reading to Her Child, a woodcut from a 19th century text, “My Gentle Mother Dear”
- Letters from the University of Minnesota collection of initial capitals


- Contemporary
- The Northeastern University husky logo
- A QR Code leading to the Huskiana website


We have created many permutations of these and other designs as we configure the ideal settings for 3D printing. We have additional designs in the pipeline, as is the case with the lasercut blocks, for when the Library reopens, and/or when we have decided upon settings for the most pristine and printer-friendly 3D prints possible on personal 3D printers.
What Does LG3D Offer to Creators, Educators, and Researchers?
In conjunction with the Huskiana Letterpress Studio, Letterpress Goes 3D offers unique opportunities for creative experimentation and hands-on engagement with archival materials. During normal semesters, Huskiana offers community hours where Northeastern community members can come to the press to work on personal projects. While Huskiana expects community members to provide their own paper for personal print jobs, Huskiana otherwise provides the letterpress materials and devices necessary to create prints — including, through LG3D, the opportunity for community members to create blocks of their own. Community members can create their own designs using our online 3D printing guide and send them to the library 3D print lab, where they can be printed for a small fee (just a few dollars). LG3D team members are also available for consultation on designs and the design process. Designs that are less personally oriented, and which might be useful for the press writ large, may be considered for laser cutting as well. In any case, 3D printing provides an exciting opportunity for creators to print a vast range of custom letterpress designs of their choosing and/or making.
LG3D and Huskiana offer similar opportunities to educators interested in incorporating the press or digital modeling into their classrooms. After the pandemic, we plan to offer classroom visits to demonstrate both Huskiana Letterpress technology and the possibilities of LG3D, including lessons on turning digital designs into 3D printed or laser cut blocks. We also are currently looking for desired designs from faculty to use in their courses, whether historical and contemporary. With these desired designs in hand, we can ensure that custom or replicated blocks will be available when press activity resumes, likely in the durable and precise laser cut wood format. Whether incorporating digital modeling into the class itself, or having a woodcut made ahead of time for a class visit, LG3D and Huskiana offer an exciting opportunity for experiential learning, giving students the ability to recreate and reprint historical works from their class, immerse themselves in course texts through acts of creation, form connections between contemporary technologies and methods and historical ones, and create designs of their own for creatively inflected projects, among other possibilities. We can provide and develop lessons and visits with instructors based on the content and structure of their future courses.
For researchers, LG3D and Huskiana allows for new modes of access to archival materials. This includes, in a way, preserving them in replicated form, as well as opening the door to exhibits utilizing replicated blocks. LG3D can grant new perspectives on archival materials through hands-on engagement throughout the letterpress process, and close attention to their visuality and materiality in both the letterpress and modeling process. As LG3D grows and continues, archival opportunities arise for the creation of a database of woodcut and metalcut designs reverse engineered for letterpress use.
Future Goals of Letterpress Goes 3D
During Spring 2020, Letterpress Goes 3D will focus on creating and refining additional instructional materials, including videos on laser cutting and 3D printing processes, and a DITI-listed Canvas page with modules focused on lessons incorporating LG3D. LG3D will also continue to develop its relationship with groups in the Northeastern campus community and with the larger letterpress community, including the Museum of Printing in Lowell, and the UCSB Broadside Ballad Archive and Letterpress Studio. We welcome Northeastern instructors and researchers to send us designs they would like to have printed for use in their classes and research. LG3D also seeks partnerships with Boston-area and other outside groups and institutions to work on robust, grant-funded research projects using the toolkits we have assembled and our unique digital-analog skillset and resources.
We encourage you to email us with questions, comments, desired designs, or potential collaborations! Contact Professor Ryan Cordell at r.cordell@northeastern.edu and Assistant Director Kenny Oravetz at oravetz.k@northeastern.edu.